Static, Couple and Dynamic Unbalance
Unbalance is a result of uneven distribution of mass, which causes the machine to vibrate. The vibration is produced by the interaction of an unbalanced mass component with the radial acceleration due to the rotation, which together generates a centrifugal force. Since the components rotate, also the force rotates and tries to move the rotor along the line of action of the force.
Static Unbalance
Static unbalance – is where the mass axis is displaced only parallel to the shaft axis. The unbalance is corrected only in one axial plane
Couple unbalance
Couple unbalance – is where the mass axis intersects the running axis. ...
Dynamic unbalance
Dynamic unbalance – is where the mass axis is not coincidental with the rotational axis. ...
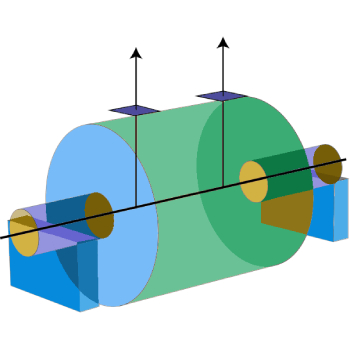
Static Unbalance
Static unbalance is an eccentricity of the center of gravity of a rotor, caused by a point mass at a certain radius from the center of rotation. An equal mass placed on the opposite side (180 deg) will balance the rotor.
Static unbalance is classified as single-plane unbalance, meaning that it is represented by a single vector quantity and corrected by a single correction mass applied opposite to the unbalance location and in the axial plane of the mass center of the rotor. When there is no way to add (or remove) mass in the same plane as the unbalance, the correction can be split into two equal corrections at the ends of the rotor to achieve the same results. Static unbalance can be detected by nonrotational equipment and is characterized by the fact that the principal axis is displaced parallel to the shaft axis,
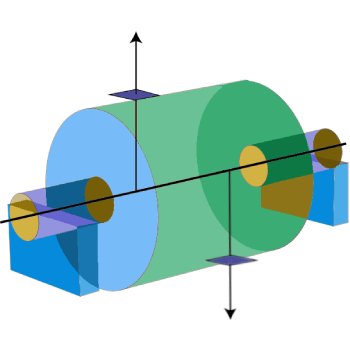
Couple unbalance
A couple of unbalances may be found in a rotor whose diameter is less than 7 to 10 times its width. In the case of a cylinder, it is possible to have two equal masses placed symmetrically about the center of gravity, but positioned at 180° from each other. The rotor is in static balance (there is no eccentricity of the center of gravity), but when the rotor turns, the two masses cause a shift in the inertia axis, so that it is no longer aligned with the rotation axis, leading to strong vibrations.
The unbalance can only be corrected by taking vibration measurements with the rotor turning and adding correction masses in two planes. Couple unbalance rotor is stationary, the end masses balance each other. However, when it rotates, a strong unbalance is experienced.
Couple Unbalance. Couple unbalance is a condition in which the principle axis intersects with the shaft axis at the center of mass (which means there is no static unbalance) but is inclined at an angle to the bearing axis, as shown in Fig.
Couple unbalance (also called moment unbalance) has equal unbalances spaced 180° from each other, at opposite ends. Generally, couple unbalance is the result of each bearing plane not being precisely perpendicular to the rotational axis. When the rotor spins, it vibrates with a twisting motion. Couple unbalance cannot be corrected in one plane; two corrections are required.
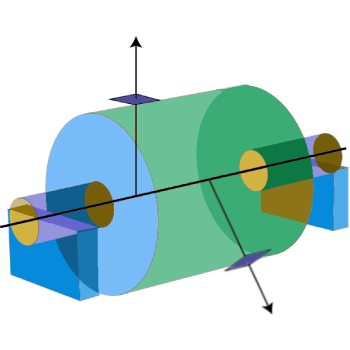
Dynamic unbalance
Dynamic unbalance is a combination of static and couple unbalance and is the most common type of unbalance found in rotors. To correct dynamic unbalance, it is necessary to make vibration measurements while the machine is running and to add balancing masses in two planes.
Dynamic Unbalance. Dynamic unbalance follows the same condition as couple unbalance and can be measured only when the part is rotating. Dynamic unbalance is present when the central principal axis of inertia neither is parallel to nor intersects the shaft axis at the center of mass. This can only be corrected in two or more planes. Dynamic unbalance is the general case of a combination of static and couple unbalance.
Quasi-Static Unbalance. In quasi-static unbalance, there is a specific combination of static and couple unbalance such that the angular position of one couple component coincides with the angular position of the static unbalance. If the axial location of the unbalance can be used for unbalance correction, then a single correction is possible. Otherwise, it must be treated the same as dynamic unbalance. In some production situations, correction can be made at a single plane close enough to the source of the unbalance to enable efficient balancing correction to within the required tolerance. This rare case of couple and static unbalance is shown in Fig.
Multiplane balancing is sometimes required when there is insufficient material or space available to make all the required unbalance corrections. In this case, a pre-balanced operation in one or two auxiliary planes precedes final balancing. In some applications where the rotors are flexible, multiplane balancing is used to minimize the rotor’s internal bending stresses.
About our services
We offer 24/7 Emergency In-House Dynamic Balancing Services at our factories at various locations in Western India, to serve any kind of Industries. One of our experienced engineers will always be on hand to take your call, no matter what time of day it is, talking to you about your balancing needs. We have decades of experience and have balanced a diverse range of rotating items in this time, including rotors, impellers, shafts, turbines, compressors etc.
Our balancing capacity
Weight: 0.5 kg to 30 tons
Diameter: upto 4 meters
Length: upto 13.5 meters
RPM: upto rated speed of 3500 RPM