What is dynamic unbalance?
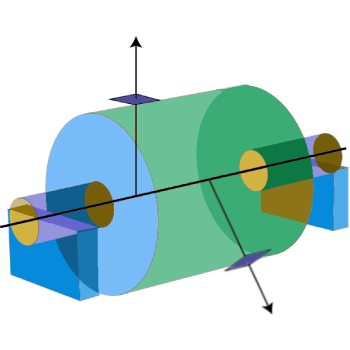
Dynamic unbalance is a combination of static and couple unbalance and is the most common type of unbalance found in rotors. To correct dynamic unbalance, it is necessary to make vibration measurements while the machine is running and to add balancing masses in two planes.
Dynamic Unbalance. Dynamic unbalance follows the same condition as couple unbalance and can be measured only when the part is rotating. Dynamic unbalance is present when the central principal axis of inertia neither is parallel to nor intersects the shaft axis at the center of mass. This can only be corrected in two or more planes. Dynamic unbalance is the general case of a combination of static and couple unbalance.
Quasi-Static Unbalance. In quasi-static unbalance, there is a specific combination of static and couple unbalance such that the angular position of one couple component coincides with the angular position of the static unbalance. If the axial location of the unbalance can be used for unbalance correction, then a single correction is possible. Otherwise, it must be treated the same as dynamic unbalance. In some production situations, correction can be made at a single plane close enough to the source of the unbalance to enable efficient balancing correction to within the required tolerance. This rare case of couple and static unbalance is shown in Fig.
Multiplane balancing is sometimes required when there is insufficient material or space available to make all the required unbalance corrections. In this case, a pre-balanced operation in one or two auxiliary planes precedes final balancing. In some applications where the rotors are flexible, multiplane balancing is used to minimize the rotor’s internal bending stresses.